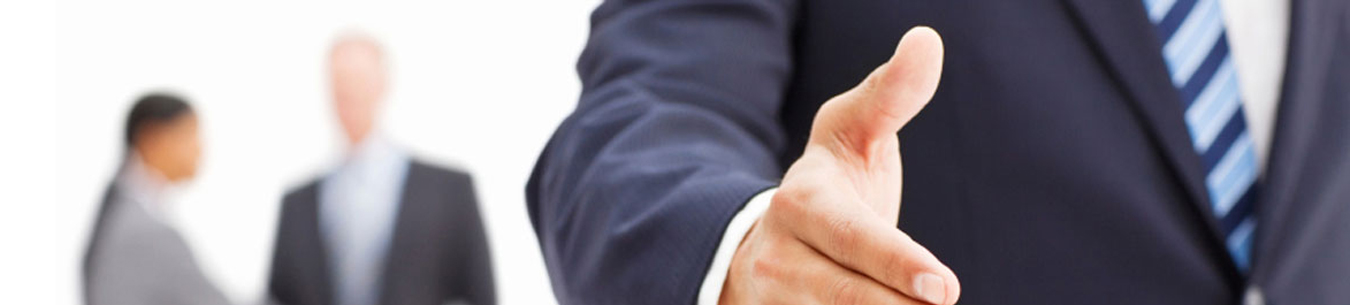
About us
OVERSEES ASSOCIATES AND LICENSORS:
Besides the Walter Craven Group, the company has also technical tie-ups with
- M/s Prago Invest Corporation of Czechoslovakia (now Czech Republic)
- M/s. Contar Plus, Prague, Czech Republic
- M/s. Gairing GmbH & Co Kg, Riedlingen, Germany
- M/s. Walter Craven GmbH, Germany
A PROJECT DIRECTLY LINKED TO INFRASTRUCTURAL INDUSTRIES CONSIDERED TO BE OF NATIONAL IMPORTANCE
In India and Bangladesh brick industry is identified as the highest polluting industry next to thermal power stations. As per the mandate of UNDP the traditional brick making activities in India – Bangladesh have to be modernised to contain pollution below the permissible limit or close down. India produces about 14000 crore bricks under the unorganised sector. The Govt. of India and also Govt. of Bangladesh have adequate funds for modernisation, mechanisation of the traditional brick making activities which once implemented will generate employment and business worth billions of rupees. Walter Craven India is the only company having the technology to manufacture, install, commission on turnkey basis the total plant from box feeder to tunnel kiln by virtue of their experience and technical collaboration with a number of renowned European companies specialised in this field.
The workshop is located at Uttarpara, near Kolkata City, West Bengal, India.
Manufacturing Capacity :
- 60 lakh bricks per line, in 200 working days a year. (Mainly for hand-made existing manufacturers who will mechanize their moulding section only)
- 1 crore to 2 crore bricks per line, in 300 working days a year with Hoffman Kiln and artificial drying system. (Semi-automatic Factory)
- 3 crore to 4 crore bricks per line, in 300 working days a year with Tunnel Kiln, automatic handling system and artificial drying system (Fully Automatic Factory)
Equipments related to
- WALTER CRAVEN SILVER X1 : 2,000 bricks per hour (modular size): Consists of: -
Box Feeder with lump breaker (ii) Conveyors (iii) Extruder with mixing unit (iv) Rotary Chain Cutter with take-off conveyor (v) Drying – natural / sun drying (vi) Firing – Modified Hoffman Kiln / Modified High Draught Kiln - WALTER CRAVEN GOLD X4 : 4,000 bricks per hour (modular size): Consists of: -
Box Feeder with lump breaker (ii) Conveyor (iii) Grinding roller (iv) Long U-mixer (v) Crusher Cleaner (vi) Rotary Chain Cutter with take-off conveyor (vii) Drying – natural / sun drying (viii) Firing – Modified Hoffman Kiln / Modified High Draught Kiln - WALTER CRAVEN PLATINUM X8 : 10,000 capacity bricks per hour (Modular size)
Box Feeder with lump breaker (ii) Conveyor (iii) Grinding mill (iv) Long U-mixer (v) Conveyor (vi) Crusher Cleaner (vii) De-airing extruder (viii) Automatic multi-wire cutters (ix) Fully automatic system for handling wet & dry bricks & return of empty laths (x) Drying – Chamber dryer (xi) Tunnel kiln (xii) Strapping system for handling-transporting finished products.
Why set up modern machines?
The size of the Indian brick market is 14,000 crores bricks per year
To overcome the problems of: -
- Raw material crisis
- Skilled labour shortage
- Labour problems
- Out-of-season and unpredictable rain
- Pollution
- Space shortage
Services
- Test raw materials to determine suitability for manufacturing burnt-clay products.
- Identify the correct technology for manufacturing the end products.Select land for the factory site, prepare layout of the factory and infrastructure.
- Supply complete plant & machinery for production of bricks, tiles etc.
- Install plant and commissioning thereof on turnkey basis.
- Provide technicians specialized in this branch of heavy clay-based industry.