BOX FEEDER


BIG PLANT |
SMALL PLANT |
|
QTY- 1 NO. Type : NON SPILL RUBBER BELT. |
QTY- 1 NO. Type : NON SPILL RUBBER BELT. |
|
COMPRISING OF: |
COMPRISING OF: |
|
Frame fabricated from rolled steel channels, Angles etc. Body fabricated from mild steel plate (side plates 5 mm thick, back plate 8 mm thick) with all over fillet welding. Moving bottom manufactured from 10-15 mm thick heavy duty belt running on impact idler rollers. The front of the driving drum is rubber lagged from improved traction to the V-Belt. The tail end belt is adjustable to obtain correct belt tension. Spring loaded scraper for effective cleaning of belt. Spill plates to fit around 3 sides of the box feeder body. |
Frame fabricated from rolled steel channels, Angles etc. Body fabricated from mild steel plate (side plates 5 mm thick, back plate 8 mm thick) with all over fillet welding. Moving bottom manufactured from 10-15 mm thick heavy duty belt running on impact idler rollers. The front of the driving drum is rubber lagged from improved traction to the V-Belt. The tail end belt is adjustable to obtain correct belt tension. Spring loaded scraper for effective cleaning of belt. Spill plates to fit around 3 sides of the box feeder body. |
TROUGHED BELT CONVEYOR


BIG PLANT |
SMALL PLANT |
|
Qty- 3 Nos |
Qty- 1 No |
|
Belt width : 1000 mm |
Belt width : 600 mm |
|
Pulley centres : 36.5 m ( approx.) |
Pulley centres : 36.5 m ( approx.) |
|
Capacity of each conveyor: 25-40 tons per hour |
Capacity of each conveyor: 20 tons per hour |
|
Fitted with : |
Fitted with : |
|
Head and tail pulleys |
Head and tail pulleys |
|
Belting |
Belting |
|
Multi-trough idler rollers grease packed for life. |
Multi-trough idler rollers grease packed for life. |
|
Supporting structure |
Supporting structure |
|
Driving motor 3.7 kW & worm gear box |
Driving motor 3.7 kW & worm gear box |
|
Discharge chute beneath the crushing rolls |
Discharge chute beneath the crushing rolls |
|
Chute to discharge material into the grinding mill |
Chute to discharge material into the grinding mill |
GRINDING MILL
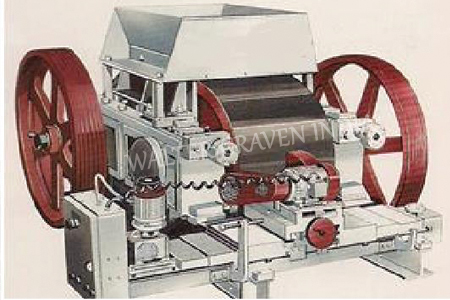

BIG PLANT |
SMALL PLANT |
|
Qty – 2 no Capacity: 25-40 tons per hour |
Qty – 1 no Capacity: 15 tons per hour |
|
General Description: |
General Description: |
|
One pair of 1000 long x 1000 dia mm heavy duty crushing rolls made from high grade Manganese cast steel alloy, duly hardened and ground. These crushing rolls are driven by separate individual motors through V –belts & pulley. Rollers are mounted with “collate” type locks to align both rolls in the same area it also allows easy removal of shells for replacement. Heavy duty spherical roller bearings in halves on the roller shafts, pulley shaft and intermediate shaft duly centralised lubricated/local lubrication by lubricating oil retainer. Complete with : DRIVE: 55 KW, 960 r.p.m TEFC FAN COOLED AC MOTOR (ONE NO.) 37 KW, 960 r.p.m. TEFC FAN COOLED AC MOTOR (ONE NO.) |
One pair of heavy duty crushing rolls made from high grade Manganese cast iron alloy, duly hardened and ground., These crushing rolls are driven by separate individual motors through V –belts & pulley. Rollers are mounted with “collate” type locks to align both rolls in the same area it also allows easy removal of shells for replacement Heavy duty spherical roller bearings in halves on the roller shafts, pulley shaft and intermediate shaft duly centralised lubricated/local lubrication by lubricating oil retainer. Complete with : DRIVE: 37 KW, 960 r.p.m TEFC FAN COOLED AC MOTOR (ONE NO.) 55 KW, 960 r.p.m. TEFC FAN COOLED AC MOTOR (ONE NO.) |
TRUING ATTACHMENT (optional)
One set of truing attachment with carbide tipped tools is provided to generate virgin surface on the roller face as and when required.
This attachment is easily replaceable type and can be fitted on either side machine for truing both the rolls. Motor rating : 0: 37 kw.
DOUBLE SHAFTED MIXER
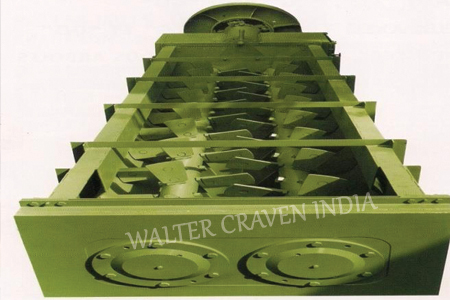

BIG PLANT |
SMALL PLANT |
|
Qty – 1 NO. Capacity : 25-40 tons per hour Trough length : 3.80 m Trough width : 1220 mm |
Qty – 1 NO. Capacity : 15 tons per hour Trough length : 1.8 m Trough width : 840 mm |
|
Fitted with : |
Fitted with : |
|
Main drive by 30 kW A.C motor through a gear box distribution gear box. Shafts of carbon forged steel Fabricated steel mixing trough 3.80 m long x 1000 mm wide Mixer knives with renewable alloy steel blades bolted to carbon steel shanks, each shank being secured in the mixer shaft by a hexagonal nut. Special augers at the discharge and if required on case to case basis. Water spray system comprising spray plugs at the rear of the mixer trough Complete with : Discharge chute for the D.S. mixer to the feed opening in extruder. Platform giving access along side of the double Shafted mixer. Access stairway from ground level. |
Main drive by 30 kW A.C motor through a gear box distribution gear box. Shafts of carbon forged steel Fabricated steel mixing trough 2.74 m long x 840 mm wide Mixer knives with renewable alloy steel blades bolted to carbon steel shanks, each shank being secured in the mixer shaft by a hexagonal nut. Water spray system comprising spray plugs at the rear of the mixer trough Complete with : Discharge chute for the D.S. mixer to the feed opening in extruder. Platform giving access along side of the double Shafted mixer. Access stairway from ground level. |
EXTRUDER with DE –AIRING SYATE
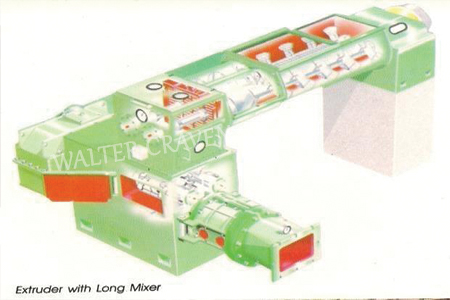
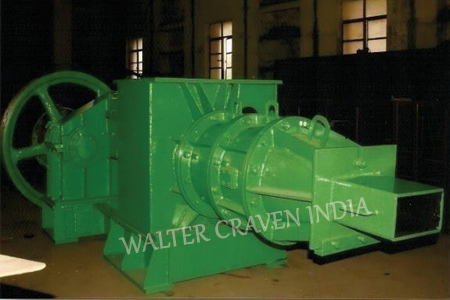
BIG PLANT |
SMALL PLANT |
|
Qty – 1 NO. Capacity : 7000-7500 std bricks per hour. |
Qty-1 no. Non de airing extruder without u mixer. Capacity : 3500-4000 std bricks per hour approx. |
|
SALIENT FEATURES: |
SALIENT FEATURES: |
|
Extra long double shafted mixer / pug sealer with trough 2000 lgx850 width. Replaceable alloy steel mixer blades fitted to steel shanks which are easily adjust for optimum angle. All wearing parts designed for maximum life and ease of re placement. Augers are made of high grade alloy steel with hardened surface. Special lubrication pump with valve, gauge and oil tank is provided for lubrication. De airing unit fitted at the appropriate location. Drive: Both mixing unit and extrusion unit is driven by separate individual motors the belt and pulley system. Motor rating of Extrusion unit- 75 kW A.C x 960 RPM Gearing: The drive to the extruder are through single reduction gears via double pinion mounted on the pulley shaft. All the gears are hardened and ground for smooth operation.. Bearing: Standard, internationally available, metric sizes of ball and roller bearings are used throughout the machine. Water Addition : Water addition are by spray pipes fitted at the rear of the mixer “on/off” control . Mixer trough : The mixed has a fabricated steel trough. Auger Section The auger sections are 400-450 mm diameter in the extrusion barrel Extrusion Barrel The Extrusion Barrel is fabricated from high quality steel. Die : Two sets of fabricated steel brick die will be provided for modular brick and standard bricks. Any other die will be charged extra. |
Fabricated / cast steel body with 14” barrel. Augers are made of high grade alloy steel with hardened surface. All wearing parts designed for maximum life and ease of re placement. Drive: Motor rating of Extrusion unit- 55 kW A.C x 960 RPM The drive has a high capacity air operated disc friction clutch fitted to the driven pulley of each unit. The clutch is arranged for push button control and operated via a solenoid control valve from Control Desk. Bearing: Standard, internationally available, metric sizes of ball and roller bearings are used throughout the machine. Auger Section : The auger sections are 350 mm diameter in the extrusion barrel Extrusion Barrel : The Extrusion Barrel is fabricated from high quality steel. Die : Two sets of fabricated steel brick die will be provided for modular brick and standard bricks. Any other die will be charged extra. |
Switch & Control Panel
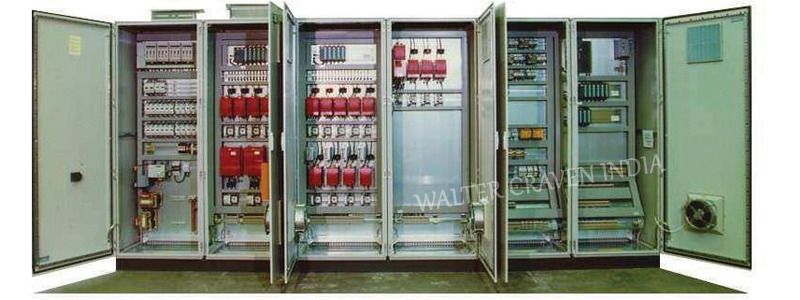
BIG PLANT |
SMALL PLANT |
|
for all electrical requirements for clay preparation and extrusion machinery consisting one complete motor control centre containing all necessary motor-starters and fuses. 1 Control desk incorporation all push buttons activators etc. |
For all electrical requirements for clay preparation and extrusion machinery consisting one complete motor control centre containing all necessary motor-starters and fuses. 1 Control desk consisting of all push buttons, activators etc. |
AUTOMATIC BRICK CUTTER
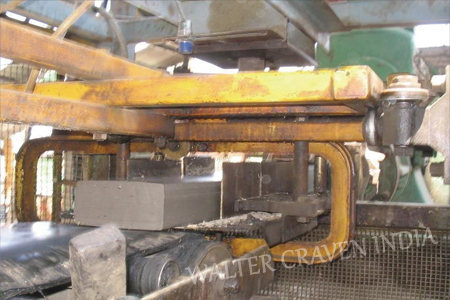
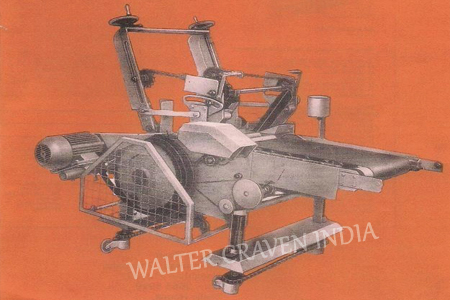
BIG PLANT |
MEDIUM PLANT |
|
Fully automatic multiwire cutte with Interlink Conveyor Rollers and Belt, Lath automat and Control Panel
|
Fully automatic Rotary Chain Cutter for cutting standard, modular size bricks and hollow blocks of different dimensions with long conveyor for manual collection of wet bricks / hollow blocks. The cutter is having its own PLC operated dedicated control panel.
|